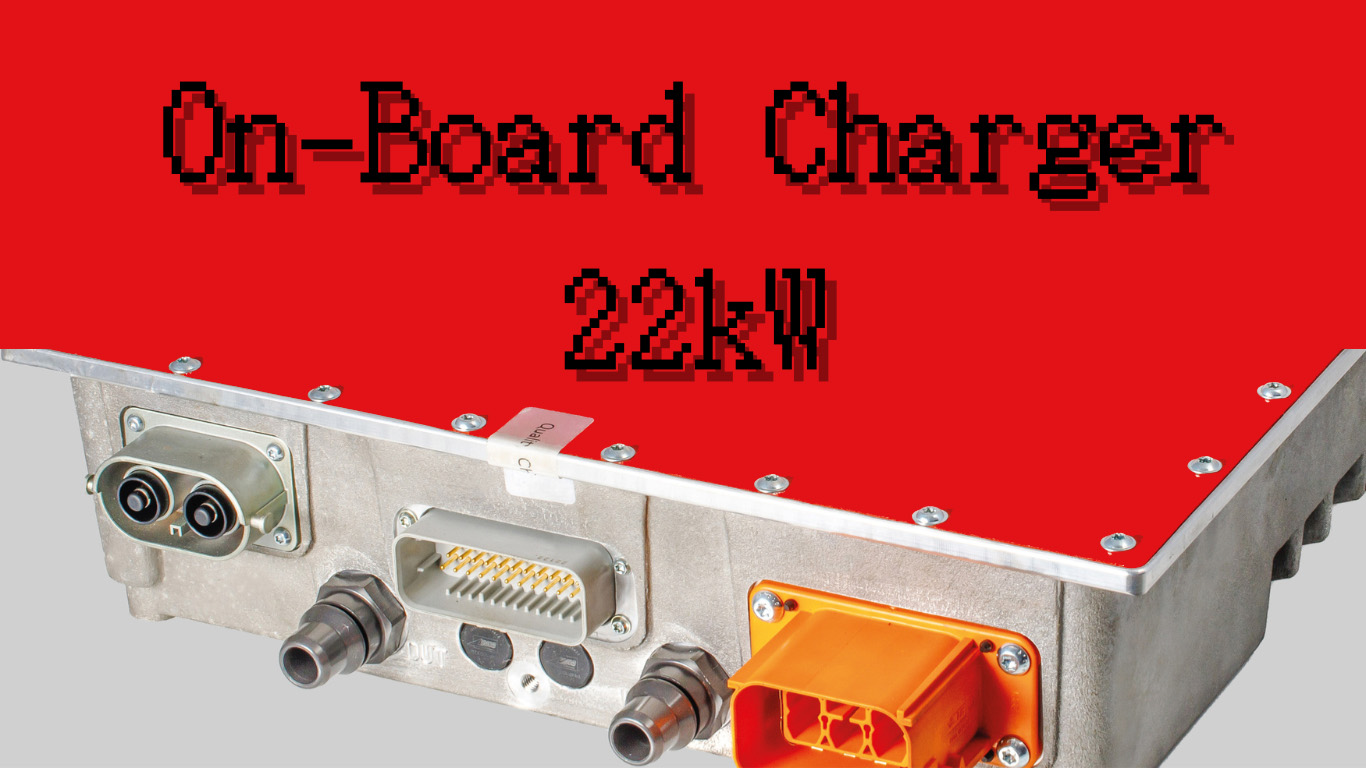
With the accelerated transformation of the global automotive industry toward electrification, the electric vehicle (EV) market is experiencing explosive growth. As one of the core supporting technologies of electric vehicles, charging technology directly impacts user experience and the widespread adoption of EVs. However, with the increasing driving range of electric vehicles and the growing demands for shorter charging times, traditional low-power on-board chargers (such as 3.3kW and 6.6kW) are gradually struggling to meet the need for rapid energy replenishment. Especially in long-distance travel and emergency charging scenarios, long charging wait times have become a bottleneck limiting the further development of electric vehicles. The 22kW on-board charger has emerged as a new generation of efficient charging equipment. By increasing the charging power, it significantly shortens charging times and brings revolutionary changes to the energy replenishment of electric vehicles. Compared to low-power chargers, a 22kW on-board charger can inject more energy within the same period. For example, for an electric vehicle with a 60kWh battery capacity, using a 7kW slow charging station requires about 8.5 hours to fully charge, while a 22kW on-board charger can reduce the charging time to under 3 hours. This greatly improves vehicle utilization, strengthens the competitive edge of electric vehicles over traditional fuel-powered cars, and provides users with a charging experience closer to that of refueling a fuel car, effectively alleviating “range anxiety” and driving electric vehicles toward becoming mainstream transportation tools. This is of significant importance for the improvement and sustainable development of the entire electric vehicle industry ecosystem. Working Principle and Key Technologies of the 22kW On-Board Charger
AC Input and Rectification
The primary task of the 22kW on-board charger is to convert AC power from the grid into DC power to meet the charging requirements of the electric vehicle's battery pack. When the charger is connected to the grid, the AC power first passes through the electromagnetic interference (EMI) filter circuit. This circuit acts as a precise filter, effectively removing high-frequency noise and electromagnetic interference from the grid, ensuring stable and pure input current for the subsequent conversion process.
Power Factor Correction (PFC)
Power factor correction is a key step for the 22kW on-board charger to improve power quality and optimize grid compatibility. If the power factor is low, it will increase harmonic distortion in the grid current, raise reactive power losses, reduce transmission efficiency, and potentially cause voltage fluctuations and overheating in the grid.
DC Conversion and Output
After rectification and power factor correction, the DC power needs to be further converted into voltage and current that meet the characteristics of the electric vehicle’s battery for efficient charging. In this stage, the DC-DC conversion circuit plays a key role, with common topologies including LLC resonant converters and phase-shift full-bridge converters.
Enhancement of Electric Vehicle Performance with the 22kW On-Board Charger
Compared with Traditional Low-Power Chargers
In the field of electric vehicle charging, charging speed is one of the key indicators for evaluating the performance of a charger, directly impacting user experience. Traditional low-power on-board chargers, such as the commonly used 3.3kW and 6.6kW chargers, take longer to charge electric vehicles due to their power limitations. For an electric vehicle with a 60kWh battery capacity, using a 3.3kW charger would require approximately 18.18 hours to fully charge (60 ÷ 3.3 = 18.18 hours). If a 6.6kW charger is used, the charging time would be approximately 9.09 hours (60 ÷ 6.6 = 9.09 hours).
On the other hand, with a 22kW OBC, the charging time can be significantly reduced to around 2.73 hours (60 ÷ 22 = 2.73 hours) under ideal conditions. This represents a reduction of nearly 15.45 hours compared to the 3.3kW charger, with an efficiency improvement of about 5.6 times, and a reduction of 6.36 hours compared to the 6.6kW charger, with an efficiency improvement of about 2.3 times. This means that owners can quickly replenish the battery during emergency travel or long trips, greatly reducing wait times, making the use of electric vehicles more convenient and closer to the refueling experience of traditional fuel cars, effectively alleviating “range anxiety.” Reducing Charging Losses and Contributing to Range
Traditional low-power chargers experience significant energy losses during the conversion and transmission process, which not only reduces charging efficiency but also indirectly impacts the vehicle’s range. Common 3.3kW or 6.6kW chargers, using basic power conversion topologies and standard silicon-based power devices, suffer considerable energy loss in the rectification, voltage conversion, and current regulation stages. For example, the conversion efficiency of a 6.6kW charger is typically between 85% and 90%, meaning 10% to 15% of the energy is lost as heat during charging. For a 50kWh battery-equipped electric vehicle, if the charging efficiency is 85%, charging from 20% to 80% would take approximately 4.3 hours ([(80% - 20%) × 50kWh] ÷ 6.6kW ÷ 85% ≈ 4.3 hours). During this time, the energy loss would be around 4.5kWh ([(80% - 20%) × 50kWh] × (1 - 85%) = 4.5kWh).
Practical Case Analysis
To better illustrate the charging speed advantages of the 22kW On Board Charger in real-world applications, a popular electric vehicle model was selected for testing. The model supports various charging power modes, and charging tests were conducted using 3.3kW, 6.6kW, and 22kW On-Board Chargers in different scenarios, recording charging times and the amount of power added. In a home slow-charging scenario, using a 3.3kW on-board charger, charging from 20% to 100% took 16 hours and 30 minutes, requiring an overnight charge to meet the next day’s travel needs. Switching to a 6.6kW home charging station reduced the charging time to 8 hours and 15 minutes, which could be completed during the night-time off-peak electricity hours but still required prior planning. When using the 22kW OnBoard charger, the charging time from 20% to 100% was reduced to just 3 hours and 20 minutes, meaning even after returning home from work, a quick charge could provide sufficient battery capacity for evening outings or morning commutes the next day. In a public fast-charging scenario, at a commercial complex parking lot, the vehicle with 30% battery left was connected to the charging station. The 3.3kW slow charger added only about 3.3kWh in 1 hour, raising the battery to 33%. The 6.6kW charger added about 6.6kWh in 1 hour, raising the battery to 36%. In contrast, the 22kW on-board charger showed its powerful performance, injecting about 22kWh in 1 hour, raising the battery to 52%, significantly increasing the vehicle’s range during a short shopping or dining break. This seamless charging experience greatly enhances the practical usability and user satisfaction of electric vehicles.
Optimizing Range Performance through Battery System Adaptation
The close collaboration between the 22kW OnBoard charger and the electric vehicle’s Battery Management System (BMS) is key to optimizing range performance. The BMS acts as the “manager” of the battery, accurately monitoring parameters such as temperature, voltage, current, and remaining capacity, ensuring the battery operates safely and efficiently. For example, the Tesla Model 3, equipped with a 22kW On Board Charger and an in-house BMS, provides an optimized charging experience. During charging, the BMS monitors the battery’s status and sends real-time data to the charger’s control unit. If the battery temperature is low, the BMS instructs the charger to preheat the battery with a small current to activate it. Once the temperature is suitable, the charging power is gradually increased to prevent damage to the battery from high current in low temperatures. When the battery is nearing full charge, the BMS switches the charger to constant voltage trickle charging mode, precisely controlling the voltage to prevent overcharging, gas generation, and excessive heat, maintaining battery health. According to actual tests, when the 22kW on-board charger and optimized BMS work together, the range of the Model 3 can increase by 8% to 12% compared to vehicles with low-power chargers and suboptimal BMS adaptation. For long-range models, this could equate to an additional 30-50 km of range, significantly extending travel distance and making long-distance driving more relaxed.